The Of Alcast Company
The Of Alcast Company
Blog Article
The Of Alcast Company
Table of ContentsThe Main Principles Of Alcast Company Unknown Facts About Alcast CompanyMore About Alcast CompanyExcitement About Alcast CompanyNot known Details About Alcast Company Our Alcast Company IdeasThe 30-Second Trick For Alcast Company
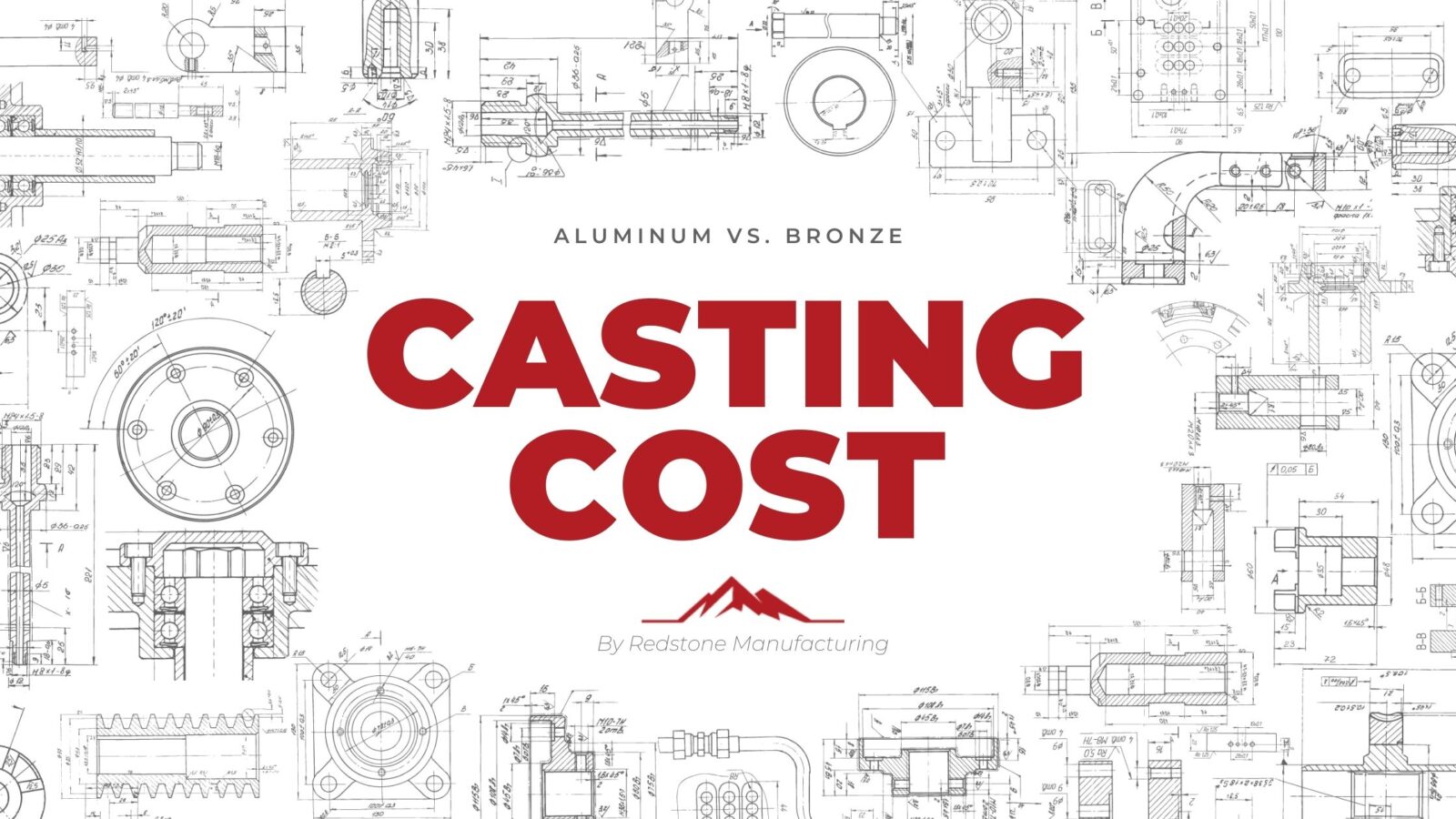
If you think that a wrought alloy may be the best for your task, have a look at a few of our write-ups that describe more concerning specific functioned alloys, such as Alloy 6061 and Alloy 6063. On the various other hand, if you assume an actors alloy would certainly be much better for you, you can discover more regarding some actors alloys in our Alloy 380 and Alloy 383 posts (coming quickly).
Not known Factual Statements About Alcast Company

Having the experience and industry understanding to craft your spreadings for optimum production and top quality outcomes will enhance the project. Producing aluminum castings requires a facility collection of processes to accomplish the best results. When choosing a new aluminum factory to partner with, ensure they have comprehensive industry experience and are well-informed about all facets of the aluminum spreading process: style, manufacturing, material analysis, and product screening.
(https://www.avitop.com/cs/members/a1castcmpny.aspx)The foundry needs to also have a tested performance history of providing remarkable products that satisfy or surpass customer assumptions. Quality assurance must additionally go to the top of your list when choosing a light weight aluminum foundry. By collaborating with a certified factory who complies with the standards for quality assurance, you can shield the stability of your product and guarantee it meets your requirements.
The Ultimate Guide To Alcast Company
By selecting a business who offers services that satisfy or exceed your product needs, you can be sure that your task will certainly be completed with the utmost precision and effectiveness. Various parts call for various manufacturing strategies to cast aluminum, such as sand spreading or pass away spreading.
Die casting is the name provided to the process of creating complex steel parts via use molds of the element, additionally called dies. The procedure makes use of non-ferrous steels which do not have iron, such as light weight aluminum, zinc and magnesium, due to the preferable properties of the steels such as reduced weight, greater conductivity, non-magnetic conductivity and resistance to deterioration.
Alcast Company Fundamentals Explained
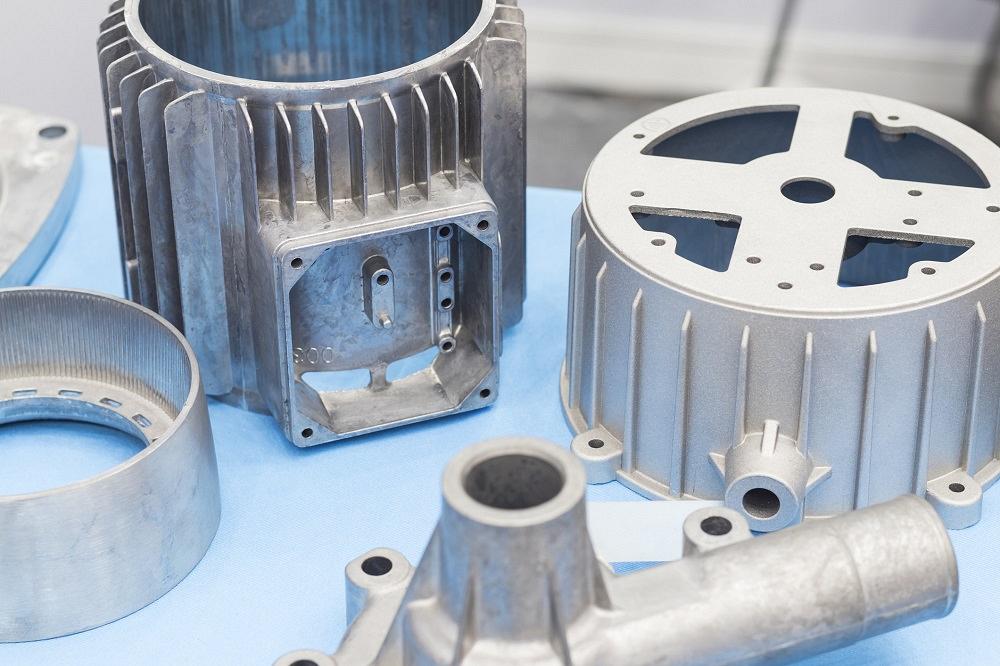
No matter the sub-process, the die casting process can be broken down right into six actions. After the pureness of the alloy is tested, dies are developed. To prepare the dies for casting, it is crucial that the passes away are clean, to make sure that no residue from previous productions stay. After cleaning, the ejection lubrication is used to the die to ensure a smooth release.
The pure metal, likewise referred to as ingot, is contributed to the furnace and maintained the molten temperature level of the metal, which is then transferred to the injection chamber and infused right into the die (aluminum metal casting). The pressure is then maintained as the steel solidifies. Once the metal strengthens, the cooling process starts
What Does Alcast Company Mean?
The thicker the wall surface of the component, the longer the cooling time since of the quantity of indoor steel that likewise requires to cool down. After the element is totally cooled, the die halves open and an ejection system presses the part out. Following the ejection, the die is closed for the following shot cycle.
The flash is the extra material that is cast throughout the procedure. This need to be cut off utilizing a trim tool to leave simply the primary element. Deburring gets rid of the smaller sized pieces, called burrs, after the trimming process. Finally, the component is polished, or burnished, to provide it a smooth surface.
What Does Alcast Company Mean?
Today, top producers make use of x-ray testing to see the entire interior of elements without reducing into them. To obtain to the completed item, there are 3 primary alloys utilized as die casting material to pick from: zinc, light weight aluminum and magnesium.
Zinc is among one of the most previously owned alloys for die casting because of its lower expense of basic materials. It's also one of the more powerful and steady steels. Plus, it has outstanding electrical and thermal conductivity. Its deterioration resistance additionally allows the elements to be long enduring, and it is just one of the a lot index more castable alloys because of its lower melting point.
The 8-Minute Rule for Alcast Company
As pointed out, this alloy is among the most generally made use of, yet makes will, at times, pick aluminum over zinc because of aluminum's production benefits. Aluminum is highly affordable and one of the much more versatile alloys. Light weight aluminum is made use of for a variety of various products and markets anything from window frameworks to aerospace products.
Report this page